Kirloskar Pneumatic turned around its stagnating gear manufacturing business by opting for the new indexable milling technology that resulted in a several hundred percent increase in productivity.
“It was critical,” Debashish Chakravarty says of the situation he found when he joined Kirloskar Pneumatic Co Ltd (KPCL) in Pune in 2010 as vice president and head of its transmission division, which makes traction gears for the sprawling Indian Railways network. “There was a huge backlog of orders of gears and pinions with late delivery charges and an extremely dissatisfied customer.”
Since a Sandvik Coromant cutter cost seven times as much as a conventional cutter, nobody wanted to take the risk, Chakravarty says. But he was convinced that the new technology was crucial to turning the division around and clearing the huge order backlog. The decision amounted to a huge leap of faith for KPCL. “There was doubt and scepticism all around,” Chakravarty says. When the additional CNC hobber and the Sandvik indexable cutter were installed, the results were apparent immediately. Instead of the usual one gear per shift, the operation was on track to turn out two or even three gears. Satisfied, Chakravarty went home.
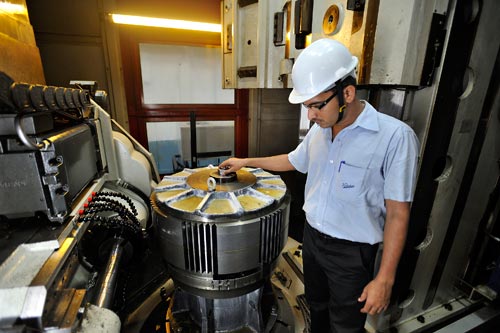
The new indexable milling cutter gave perfect results from the get-go. Today Kirloskar Pneumatic uses 14 Sandvik Coromant
cutters.
While the naysayers around him looked on, Chakravarty received an immediate replacement from Sandvik Coromant free of charge. “It gave perfect results,” he says. Four weeks later the cutter returned, and Chakravarty says that for a time he had two cutters. Gear production jumped from 190 a month to 450, and Sandvik Coromant established both goodwill and trust.
After the first year, the cutting time for a gear had been reduced from 6.5 hours to just 45 minutes. “Nobody could believe it,” Chakravarty says.
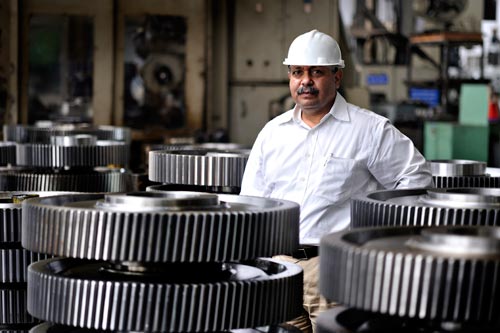
With new indexable milling technology, Kirloskar Pneumatic Vice President Debashish Chakravarty got a higher output.
He started using indexable cutters for other railway components, and today he uses 14 Sandvik cutters. Profitability has doubled. Sandvik Coromant representatives work jointly with his operation, modifying or changing things when necessary. “They give complete solutions and are reliable and transparent,” he says. “When something is not possible, they tell us.”
Now Chakravarty is working on a cutting solution that will be even faster – a Sandvik Coromant indexable hob.
Courtesy: Sandvik Coromant