By beginning of the year, DMG MORI will once again underline its high level of innovation at the Open House at DECKEL MAHO in Pfronten.
As has become tradition, the focus of the DMG MORI Open House event at DECKEL MAHO Pfronten from 26th to 30th January 2016 will be on the latest innovations and groundbreaking technologies. On an exhibition area of 7,400 m², the machine tool manufacturer will be showcasing in total 90 high-tech exhibits live in operation, thereof the DMG MORI best-sellers as well as six world premières featuring turn-mill complete machining, universal milling, XXL parts machining and new technologies.
Besides innovative production and automation solutions, with CELOS® and DMG MORI technology cycles, DMG MORI will be giving answers to the question of digitisation on the path to intelligent production in Industry 4.0.
CELOS® & DMG MORI Technology cycles for Industry 4.0
With CELOS®, DMG MORI is offering a cutting-edge user interface that can be expanded with new APPs and updates and which provides an immediate solution to Industry 4.0. CELOS® is as easy to use as your smartphone, networks all machines within a manufacturing organisation and therefore simplifies the process from the idea to the finished product. 16 APPs help the operator prepare, optimise and process production jobs without any errors and enables the consistent administration, documentation and visualisation of order, process and machine data, consequently holistically improves the profitability of production.

DMG MORI technology cycles
Software solutions to make complex machining processes an effortless reality
World première: CTX gamma 3000 TC 2nd Generation
A turning length of 3,050 mm makes the CTX gamma 3000 TC 2nd Generation the largest turn & mill complete machining centre in the now completely revised CTX TC series from DMG MORI. Like its smaller sister models the machine tool manufacturer has also equipped this latest machine with a new compactMASTER® mill-turn spindle, which with 220 Nm achieves a 120 percent higher torque.
With a diameter of 202 mm the length of the compactMASTER® spindle has been reduced by 70 mm so that it now measures only 450 mm. The interplay of the 150-mm larger X-axis (-25 / +175 mm) and the 20-mm longer Y-travel of ± 210 mm brings an enormous gain in freedom for users. This enables, for example, the radial machining of workpieces with maximum diameters of 700 mm with 170-mm long tools (with the B-axis in a vertical position). With regard to other equipment features, the CTX gamma 3000 TC 2nd Generation is equipped with 36 tool pockets in its standard version. This capacity can be increased optionally to 80, 120 or 180 tools. Maximum tool length here is 550 mm.
World première: DMU 160 P duoBLOCK® 4th Generation
The world première of the DMU 160 P duoBLOCK® 4th Generation impressively complements the successful duoBLOCK® series from DMG MORI and excels for its world première with remarkable improvements in precision, performance and efficiency of around 30 percent. In addition the revised machine concept offers a clear plus in versatility. Added to this the high level of rigidity, extensive modular spindle range and innovative cooling measures ensure perfect machining performance and a high degree of long-term accuracy. Equipped with CELOS® the machine also guarantees user-friendly production.

World première: DMU 210 P 2nd Generation
The DMU 210 P 2nd Generation with its optimised work area, which now measures 2,100 x 2,100 x 1,250 mm, is the prelude to the new generation of portal machines from DMG MORI. A considerably higher level of rigidity and an intelligent cooling concept that includes a spindle growth sensor ensure maximum long-term accuracy for the DMU 210 P 2nd Generation, making it significantly more accurate than its predecessor does.

World première: DMU 210 P 2nd Generation
2nd generation with 5X torqueMASTER® for maximum cutting power with 1,300 Nm torque
World première: DMU 600 G linear
In the XXL Centre at DECKEL MAHO in Pfronten – the most cutting-edge large machine production in the world – DMG MORI designed and constructed the DMU 600 G linear for best surface quality and high dynamics. These are achieved through the use of the innovative contactless linear-motor drive technology. The design of the machine has been optimised with regard to static and dynamic rigidity and ensures consistent temperature stability thanks to extensive temperature control measures for the structure, components and guides. Energy-efficient consumption is achieved by the use of innovative cooling technology and needs-based activation of units.
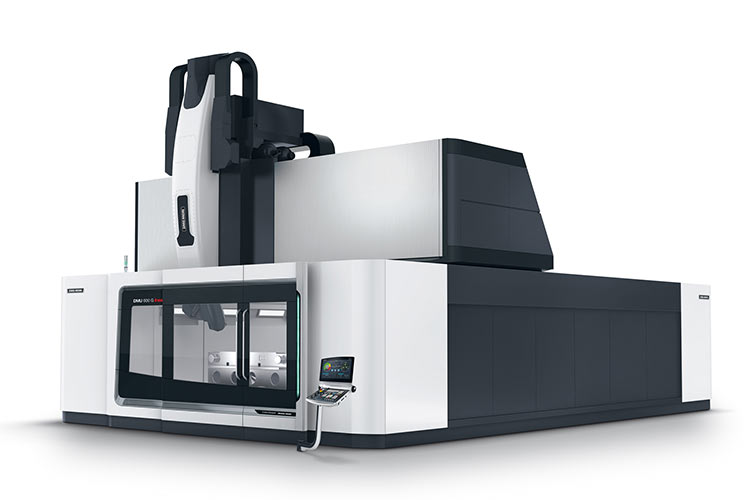
World première: DMU 600 G linear
Gantry machine with linear drives in the X, Y and Z axes for unrivalled surface quality
World première: DIXI 125
DMG MORI has extended the high-precision machining centres in the DIXI series to include the smaller DIXI 125 for workpieces with diameters up to 1,250 mm. Like its bigger sister models the DIXI 125 also impresses with a unique volumetric accuracy of less than 15 µm. The basis for this are the manually scraped guide contact surfaces that achieve a flatness and straightness of three µm when mounted, perfect machine geometry and on-site volumetric measurement and compensation.

World première: CTX gamma 3000 TC 2nd Generation
800 mm X travel with the new compactMASTER® turn-mill spindle rated at 220 Nm torque
World première: ULTRASONIC 20 linear 2nd Generation
Even externally, the completely revised ULTRASONIC 20 linear 2nd Generation with its new, functional design and a reduced footprint of just 3.5 m² is impressive compared to its predecessor. The diverse technological optimisations include the now optional 60,000 rpm speed of the spindle, the up to 47 percent (A-axis) more powerful drive motors, a 15-kg higher load weight and the use of larger tool diameters of up to 50 mm. Another highlight is the high-speed C-axis (1,500 rpm) for high-precision and productive internal and external cylindrical grinding of rotational-symmetric workpieces made of advance materials.
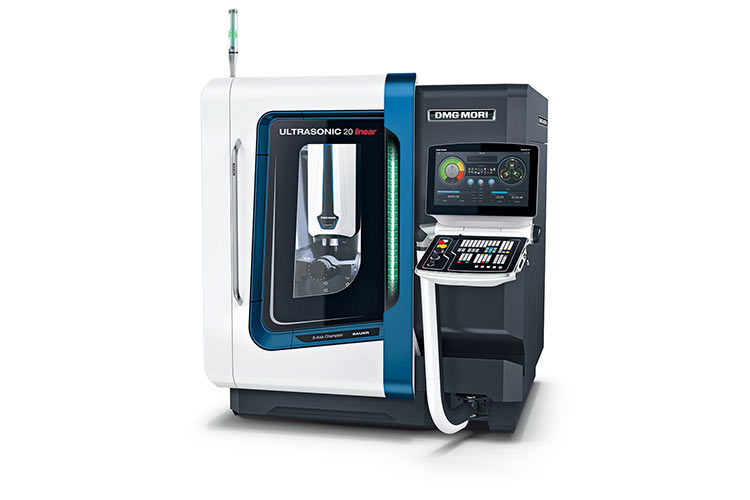
World première: ULTRASONIC 20 linear 2nd Generation
Highly compact 5-axis grinding of advanced materials as well as the latest generation HSC milling